|
We introduced "What are the advantages and uses of POM?" In the previous article, and in this article we continue to understand the precautions for POM injection molding. The process conditions for injection molding include the following:
1. Drying: The resin itself has very low hygroscopicity, so it does not necessarily need to be dried. However, if the moisture content is greater than 0.1% during molding, it needs to be dried, which is also helpful to avoid mold scale. Carbon fiber filled, conductive grades must be dried. The drying conditions are 80-90 ° C, 3 ~ 4 hours.
2. Recycling: Recycled materials can be used. Even if the recycled material is used 100% for 10 times, its physical properties will not basically change, but the color will change. In principle, 25-30% of recycled material is mixed with 75-70% of new material.
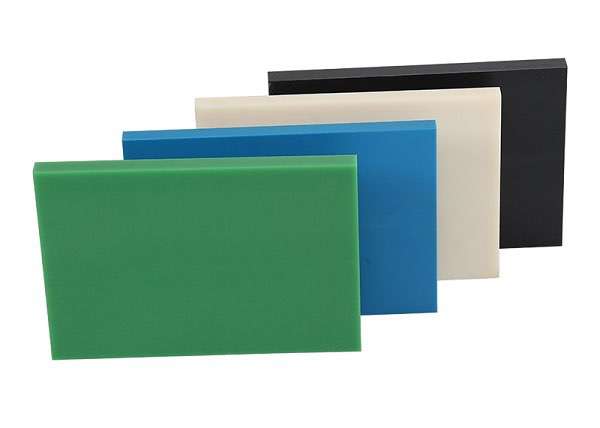
3. Thermal stability: After staying at 210 ° C for 60 minutes and then molding, the tensile strength of the molded product has hardly changed. Has good thermal stability.
4. Injection machine table: Use ordinary injection molding, clamping force> projected area of molded product x40-60MPa.
5. Barrel capacity: The product weight is generally 40-80% of the barrel capacity.
6. Nozzle and latching system: Open nozzles are available, but in order to prevent drooling, it is best to use latching nozzles.
7. Screw: Just use standard screw, compression ratio 2.8-3.0: 1, length-diameter ratio: 18-22: 1.
8. Barrel temperature: The melting point of the resin is about 165 ° C. The optimal temperature for actual molding is 190-210 ° C, preferably 200-210 ° C.
9. Mold temperature: The standard mold temperature is 60-80 ° C. Depending on the characteristics of the molded product, surface conditions, size changes during use, molding cycle and other requirements are different. The mold temperature needs to be adjusted. Sometimes, in order to reduce the molding cycle, the mold temperature is set at 30-40 ° C, but it is easy to leave residual strain and not obtain a good appearance.
10. Injection pressure: It should be set in consideration of the fluidity, shrinkage, and physical properties of the molded product. Generally above 98MPa. Holding pressure is 49-98MPa.
11. Injection speed: generally 5-50mm / s, but it should be set in consideration of the shape, wall thickness, quality requirements, runner thickness, gate size and other factors of the molded product.
12. Back pressure: In order to measure the stabilization and prevent dripping of the nozzle, it is recommended to set the back pressure to 0.5-1.0MPa.
13. Screw speed: Generally, 100-150rpm is appropriate.
14. Mold shrinkage: The mold shrinkage is large, which can be as high as 2-3.5%.
15. Secondary processing: engraving, tapping, pressing, metal inserts, cutting and other secondary processing can be performed.
|
|